The aerospace sector has driven composite growth in recent years due to the advantages the materials offer in the performance of both commercial and defense aircraft. Composites’ lightweight characteristics offer significant reductions in fuel consumption and carbon dioxide emissions, a key consideration in today’s climate-conscious world.
The development of lightweight and high-temperature resistant composite materials is expected to continue driving new high-performance, economical aircraft designs. But along with enjoying the improved performance, operators will have to be aware of new challenges in maintaining the materials.
UNDERSTANDING COMPOSITES
Composites are composed of strong materials embedded in relatively weak materials. Since they were first used by military operators in World War II, composites have evolved rapidly over the last 80 years. The strong, embedded portion is often referred to as the reinforcement, while the surrounding material is known as the matrix. Reinforcement can take the form of long fibers, short fibers, whiskers or particles. In most aerospace applications, long fibers are used. These reinforcing fibers improve the physical characteristics of the weak material, allowing the overall component to support structural loads without adding excess weight. Composite materials can also be molded into complex shapes using a variety of different manufacturing processes.
The modern aerospace industry uses several different fiber types: carbon fibers, glass fibers and aramid fibers, which are commonly referred to by their tradenames Kevlar® and Nomex®. There are two main types of polymer matrix materials, thermosetting or thermoplastic resins. Thermosetting resins, or thermosets, are more common due to their lower cost and high thermal resistance. However, they have short shelf lives and their manufacturing process is irreversible, making recycling challenging. Thermoplastics are more expensive and are less stable at higher temperatures. This behavior however enables them to be remelted and therefore more easily recycled.
In terms of finished composite products, carbon fiber reinforced polymers offer the highest specific strength; their strength-to-weight ratio. As a result, they are most prevalent for aerospace structures. Glass fiber reinforced polymers have lower specific strength but are much cheaper. In aerospace applications they are used for specific applications, for instance radomes. Aramid fiber reinforced polymers have high toughness, heat resistance and wear resistance, so sit separately from the other two. They are commonly used as a honeycomb core material.
Fiberglass was the earliest and most commonly used composite in aerospace applications, accounting for about 2 percent of the Boeing 707’s structure in the late 1950s. Today, composites make up about 50 percent of the Boeing 787 by weight, or 80 percent by volume. Modern composites are, however, still susceptible to environmental damage by sunlight and condensation, both of which can attack the matrix and weaken the bonds throughout a component. While early composite manufacturers and users were concerned about the materials’ reaction to fatigue, studies and in-service data over the past several decades have shown they can withstand repeated regular use.
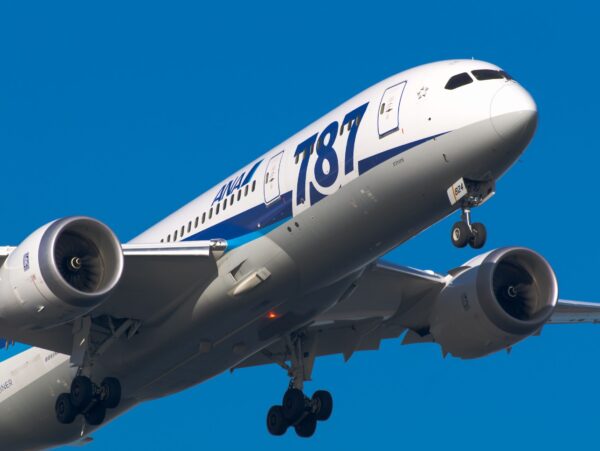
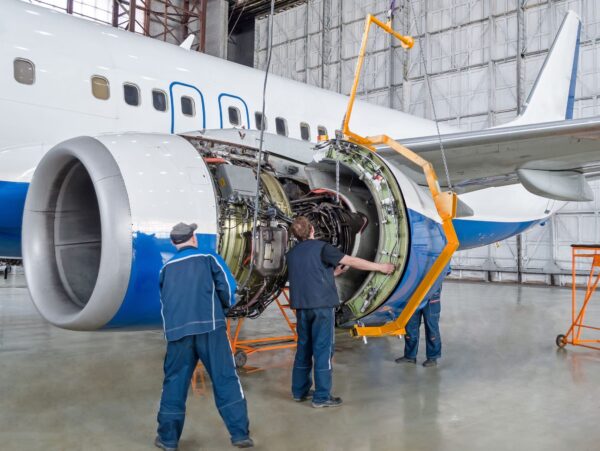
PROS & CONS
Weighing significantly less than their aluminum counterparts, advanced composite rotor blades have grown popular among helicopter manufacturers. Airbus, for example, has adopted the technology for its new H125 and five-blade H145 helicopter platforms.
Airbus manufactures its H145 blades using glass fibers, which offer high physical resistance characteristics while supporting the especially long blades’ unique geometry. When deploying longer blades, manufacturers must minimize weight not only to increase aircraft load capacity, but also to help reduce engine wear and tear. Constructed properly, lighter composite blades can lead to improved fuel efficiency, reduced running costs and environmental benefits. Airbus says the H145’s five-blade configuration offers 330 pounds of additional useful load while enhancing in-flight comfort. The improvements are especially useful for public safety aircraft operating in the air ambulance role.
The downside of composite materials is that they don’t show damage in the same way metals do. Impact damage that would cause visible dents in traditional aluminum airframes will instead cause sub-surface delaminations that may not have any surface-breaking feature. This phenomenon, known as Barely Visible Impact Damage (BVID), presents new challenges for maintenance professionals who rely on traditional inspection methods.
As well as BVID, composites are also susceptible to hidden cracks and defects that may occur during manufacturing or service. To ensure carbon fiber aircraft’s continued safe performance, non-destructive testing (NDT) is therefore critical throughout the airframe lifecycle, from prototyping and qualifying new materials to in-service inspections of aircraft structures and engines. Volumetric NDT techniques, such as ultrasonic testing, allow technicians to detect internal cracking, disbonding, and other defects potentially affecting safety and performance.
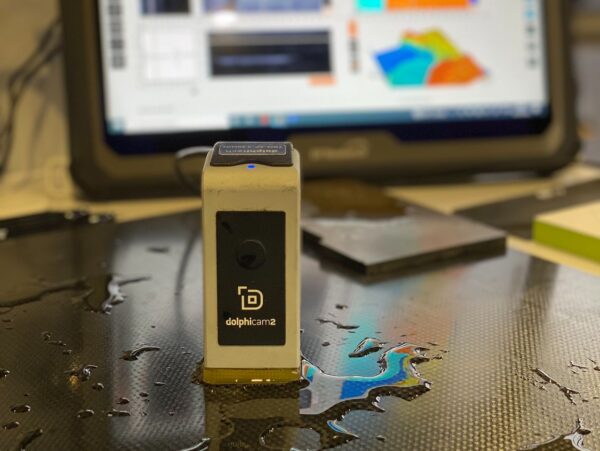
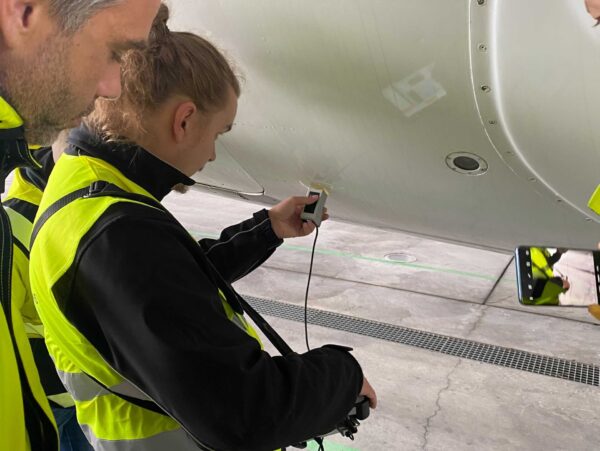
SOLVING THE PROBLEM
As aircraft operators use platforms with increasing amounts of composites, they must rely more heavily on NDT. Increased use of composites requires an increased need for non-destructive testing to maintain and safeguard the integrity of aerospace assets. Dolphitech NDT platforms are a proven solution in the aerospace industry for both manufacturing and maintenance non destructive testing. Despite the challenges mentioned above for inspecting composite materials, the dolphicam2 platform tackles these with ease. Whether it’s inspection in the field or manufacturing quality control, the platform provides reliability and accuracy that is unrivalled.
The dolphicam2, is approved by two of the world’s leading aircraft manufacturers; Boeing has authorised specific NDT procedures for their 787 aeroplanes and Airbus has accepted the dolphicam2 for all composite inspections on its assets. As with all airline operators less down time is essential (especially aircraft that are used by the police or medical services), therefore identifying flaws is critical for quick decision making.
You would be forgiven for thinking that such an effective platform with over sixteen thousand active elements, producing live C-scan, B-scan, and 3-D data would be complicated to use. However, the dolphicam2 can be set up and ready to inspect in as little as 60 seconds enabling rapid evaluation for less down time. Not only this, but the user-friendly software also means that technicians of all experience levels can generate analysis-ready images of materials in real-time for quick decision making. Having all this valuable data digitally enables records to be kept safely and securely online for future records. This approach changes the face of mission-critical NDT inspections for composites making it far simpler.
Weighing in at 3kg for the whole system, the dolphicam2 is easily portable and when combined with a continuous use battery life of 5-6 hours, makes it well-suited to life on site. Useful features include integrated neck strap, corner bumpers, plug protection shields and an IP66 ingress protection rating. All of this and an operational temperature range of -20 to +50°C means that the dolphicam2 is relied on for routine use in both indoor and outdoor industrial settings.
THE FUTURE
As we look towards the future, the aerospace industry will continue developing stronger, lighter, and more durable materials than those previously been used to build aircraft in the last century. This will ensure the aircraft of the future will be even safer, more fuel-efficient and will have a much longer lifespan. The future of the composite industry will be an exciting one to watch and we expect it will play a major role in the design and manufacture of many products and structures used. Eventually, we may see aircraft constructed entirely of composite rather than metal, but until then, having one NDT platform that can inspect metals and composites alike, such as the dolphicam2, will help provide quality assurance, minimise loss of revenue and the need for expensive repairs and replacements.
For more information on our Ultrasonic NDT solutions visit our products page.